Concrete Work for Gate Foundations in Santa Monica CA
A proper concrete foundation is the unsung hero behind every smoothly operating automatic gate system. At OnTime Automatic Gate Repair in Santa Monica, we've established our reputation by understanding that even the most sophisticated gate mechanism will fail prematurely without a properly engineered foundation beneath it.
Our concrete work for gate foundations service is specifically designed for Southern California's unique coastal conditions. We account for Santa Monica's soil composition, proximity to saltwater, seismic considerations, and local building codes when designing your gate's foundation. This specialized knowledge translates into foundations that withstand decades of continuous operation without settling, cracking, or shifting.
Every foundation we construct incorporates strategic reinforcement patterns, appropriate depth measurements for your specific gate weight, and integrated conduit systems for seamless electrical installation. We meticulously prepare the excavation site, ensuring proper drainage that prevents future erosion.
For sloped properties, our stepped foundation designs maintain perfect gate alignment regardless of terrain challenges. We can also resolve existing gate issues through foundation reconstruction, effectively eliminating sagging and misalignment problems at their source.
OnTime's concrete foundation work isn't merely about pouring concrete – it's about engineering a permanent platform that ensures your automatic gate operates flawlessly through years of daily use. Our foundations form the invisible but essential infrastructure that supports your property's security and convenience.
Our Concrete Work Services
We specialize in providing high-quality concrete work for gate foundations, ensuring durability and stability for your automatic gates. Our expertise covers a range of foundation types and careful material selection to meet various needs.
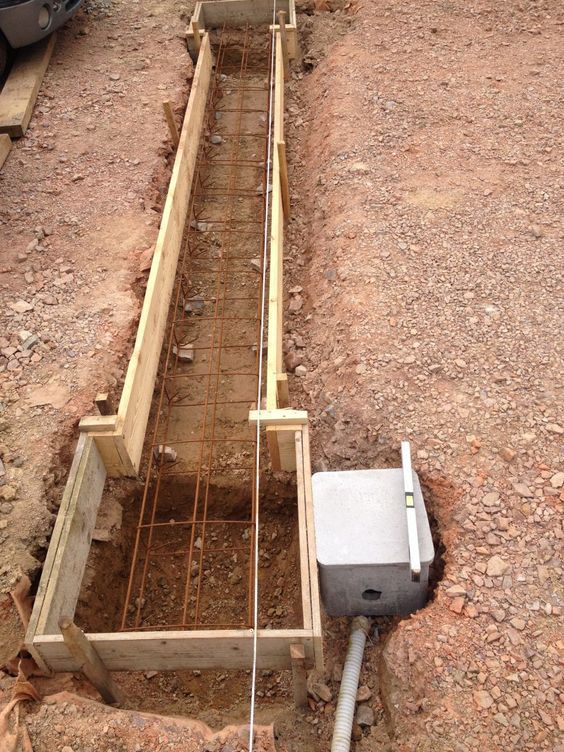
Types of Gate Foundations We Install
We offer several types of gate foundations tailored to specific gate designs and soil conditions.

- Concrete Footings: These are essential for robust support, particularly for heavy gates. We pour concrete footings that are deep enough to withstand shifting and settling.
- Slab Foundations: Ideal for lighter gate systems, these foundations provide a level surface that enhances installation accuracy.
- Pier Foundations: This option is suitable for uneven terrain. We place concrete piers at strategic points to distribute weight effectively.
Each foundation type is designed to withstand local weather conditions and the demands of daily use, ensuring longevity and reliable performance.
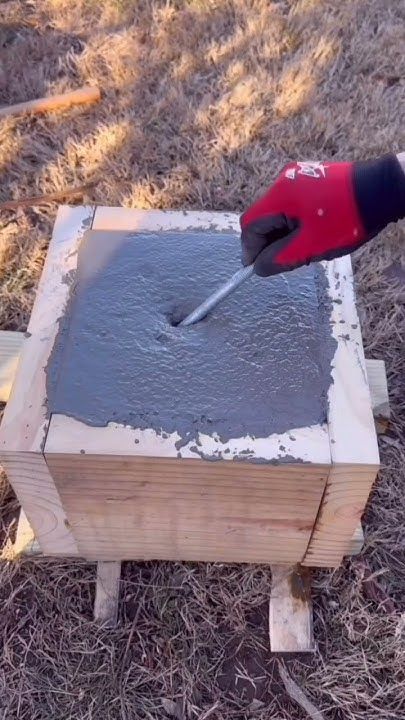
Material Selection
Choosing the right materials is crucial for gate foundations. We use high-strength concrete designed to resist cracking and weather-related wear.
Key considerations include:
- Reinforcement: We incorporate steel rebar to enhance the durability of our concrete structures. This technique helps prevent structural failures due to stress and weight.
- Mix Design: Our concrete mix includes additives that improve resistance to moisture and temperature fluctuations. This ensures that our foundations hold up well throughout the seasons.
By focusing on quality materials and construction methods, we create foundations that stand the test of time, providing a solid base for your gates.
Our Project Approach
We take a structured approach to concrete work for gate foundations, ensuring that each project proceeds smoothly and efficiently. Our method emphasizes careful evaluation, strict timelines, and maintaining a safe work environment.
1. Site Evaluation
Before any installation begins, we conduct a thorough site evaluation. This involves assessing soil conditions, determining the appropriate foundation depth, and identifying any potential obstacles.
We also check for underground utilities and ensure compliance with local regulations. By preparing the site correctly, we minimize delays and avoid additional costs later in the project.

Preparation includes clearing the area of debris and vegetation. We use heavy machinery if necessary to ensure the site is level and ready for foundation work.
2. Foundation Installation
We understand the importance of timely project completion. Our typical timeline for foundation installation spans several phases, starting from the initial site assessment to the final concrete pour.
- Day 1-2: Site evaluation and preparation.
- Day 3: Formwork setup and reinforcement installation.
- Day 4: Concrete pouring.
- Day 5: Curing time and quality checks.
Each phase is carefully scheduled to prevent overlaps, providing a clear pathway from start to finish. We communicate our timeline to clients, ensuring they are informed every step of the way.
3. Maintaining Clean and Safe Worksites
Safety is a top priority in our operations. We adhere to OSHA regulations and implement best practices for maintaining clean worksites.
We ensure that all tools and materials are stored safely and that the area is clear of hazards. We conduct daily inspections to address any safety concerns swiftly.
During the project, we also minimize noise and dust, which helps maintain a comfortable environment for both workers and nearby residents. Our commitment to cleanliness and safety ensures that projects proceed without incident and with minimal disruption.
Why Choose Us
We bring a unique combination of specialized knowledge and local expertise to every concrete foundation project. Our dedication to quality and safety sets us apart, ensuring that our clients receive the best service possible.
Experienced Technicians
We have years of experience specifically in concrete work for gate foundations. Our skilled team understands the nuances involved in laying a solid base for your automatic gates. We use high-quality materials and advanced techniques to ensure durability and longevity. This expertise minimizes the risk of future repairs and enhances the overall efficiency of your gate system.

Quality and Safety
Quality and safety are at the forefront of everything we do. We adhere to strict safety protocols during every phase of the construction process. This commitment protects both our team and your property from potential risks. Using top-grade materials ensures that the foundations we construct will withstand the test of time. We regularly inspect our work to ensure it meets our high standards.

Local Experience
Being based in Santa Monica, CA, we know the local landscape and environmental factors that may affect concrete work. Our familiarity with local regulations and building codes allows us to navigate any compliance issues efficiently. We are dedicated to serving our community and understand the specific needs and preferences of homeowners in this area. This local perspective helps us deliver solutions that fit seamlessly into your property.
FAQs on Concrete Work for Gate Foundations
We understand that making informed decisions about gate foundations is important. Below are some common questions we receive about the installation process and costs associated with our concrete work.
How much does concrete foundation work for automatic gates cost in Santa Monica?
Concrete foundation work for automatic gates in Santa Monica typically costs between $1,200-$3,000. Standard residential foundations (4-6 feet wide) average $1,500, while larger or commercial foundations can reach $2,500-$3,000. Factors affecting cost include size requirements, soil conditions, slope challenges, drainage needs, and permit fees. Premium finishes or decorative concrete may add $300-$500 to the total cost.
How long does it take to complete concrete work for a gate foundation?
A typical gate foundation project takes 3-5 days from start to finish. This includes 1 day for excavation and form building, 1 day for reinforcement placement and concrete pouring, and 2-3 days for proper curing before installing gate equipment. Weather conditions and soil complexity can extend this timeline, particularly during wet seasons. Most residential projects are completed within one week.
Can you install conduit for electrical wiring during foundation construction?
Yes, we install electrical conduit during foundation construction as a standard practice. We place appropriate-sized PVC conduits (typically 1-2 inches in diameter) at the correct depth and position for future wiring needs, including power supply, control wiring, safety sensors, access control systems, and lighting. This integrated approach prevents the need for destructive retrofitting later and ensures all electrical components meet code requirements.
How do you address foundation issues for gates on sloped driveways?
For sloped driveways, we implement stepped foundation designs with proper reinforcement to ensure stability. Our approach includes:
- Creating level pad areas for operator placement
- Installing additional drainage systems to prevent water accumulation
- Using deeper foundations on the downhill side
- Incorporating retaining elements where necessary
- Adding extra concrete mass and reinforcement to counteract lateral pressure
- Ensuring proper gate clearance throughout the swing or slide path
Can concrete foundations solve my sagging/misaligned gate problems?
Yes, properly designed concrete foundations can resolve sagging and misalignment issues. Sagging gates typically result from inadequate foundation support or post movement. We address this by:
- Installing deeper, wider foundations with proper load distribution
- Using engineered reinforcement patterns to prevent settling
- Creating solid anchor points with proper hardware embedment
- Ensuring foundations extend below frost line and unstable soil layers
- Implementing drainage solutions to prevent soil erosion around foundation areas
New foundations eliminate the underlying causes of misalignment rather than just treating symptoms.
Contact Us Today!
We are ready to help you navigate the permit process for automatic gate repair in Santa Monica. Our team understands local regulations and ensures your project meets all compliance standards.